How can you be sure that inertia friction welding will benefit your application? Below are some ways you can take advantage of inertia welding.
Â
1. Combines a variety of metals
This process is able to weld a variety of metals that can’t be joined through traditional welding. For example, your application may require (expensive) corrosion resistant materials. However, it might be unnecessary for your entire component to be resistant. Inertia welding allows you combine corrosion resistant materials with less resistant materials where there is no need. (Of course, inertia welding can also combine similar metals as well.)
2. Reduces need for expensive materials
As a result of reducing the amount of expensive materials used, inertia welding can significantly lower cost without sacrificing quality.
3. Minimizes heat affected zones (HAZ)
Friction welding minimizes heat affected zones. In other words, material properties are less affected, leaving you with a cleaner finish that’s ready-to-go (thus, decreasing production time).
4. Creates strong, airtight bond
Inertia welding joins materials together in a way that allows the full surface of the cross section to consist of both metals. The mechanical intermixing and solidification of the two metals is robust, airtight, and absent of voids and porosity.
Advantages of inertia Friction Welding compared to traditional welding
1. Significantly Reduced Cycle Time
It’s hard to overstate how significantly cycle time is reduced by using a friction welding process.
– Machine controlled process
The factors that are key in regulating the weld (rotational speed, flywheel mass, and thrust force) are machine controlled, resulting in minimal (if any) variation between each product, unlike MIG or TIG welding processes.
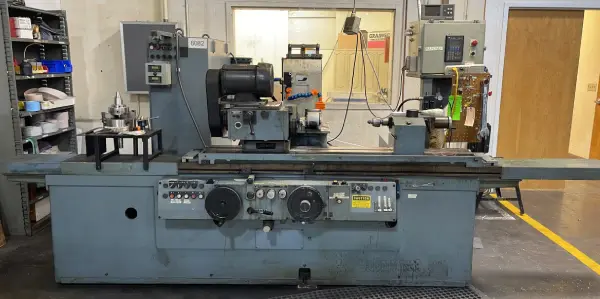
– Extreme consistency and repeatability
Once these factors are determined (a quick process for experienced welders), a component can be rapidly reproduced with little interruption in the process, creating extreme consistency and repeatability for nearly any project.
– Minimal preparation of components
A minimally prepared saw-cut surface is suitable for the inertia friction welding process because the displacement of plastic metal eliminates original surface conditions and expels any contaminants from the weld zone.
– Minimal post-welding machining required
The inertia friction welding technique produces near-net shape components that require minimal post-machining. In some cases, a ring of flash metal at the joint may have to be removed.
– Overall faster turnaround time
Simply put, the inertia friction welding process just doesn’t take very long compared to traditional welding or machining techniques.
2. Joining Dissimilar Metals
Normally, the large discrepancy between the melting points of two dissimilar metals (e.g. stainless steel and aluminium; copper and steel) would make them impossible to weld using traditional techniques, and would require some kind of mechanical connection.
The inertia friction welding process does not require the facing surfaces to melt, so when the work pieces become plasticized, pressed together and then cooled (with adjacent non-heated metal acting like a heat sink), the metals form a high-integrity bond with no alloying of the material.
The ability to choose dissimilar metals for a component allows the manufacturer to eliminate the use of expensive metals in parts of the work piece that do not require such a metal.
Not only does this reduce the material cost of the welding process, it can also help the application run more efficiently since the burden of the heavier material is reduced.
3. Cost Reductions Compared to Traditional Welding and CNC Machining
Serious savings are achieved through the inertia friction welding process in both labor hours and material costs.
– Dissimilar metals creates savings
As mentioned, the ability to utilize dissimilar metals can help manufacturers save on material costs by eliminating the need to use expensive metals throughout the entire component.
– Reduced material costs, reduced machining costs
The process requires less raw materials to achieve the same fatigue and torque thresholds of parts formed with other methods. This means a reduction in both raw materials costs and post-welding machining time to remove extra material.
– Minimal scrap material
Compared to components manufactured with a CNC lathe, inertia friction welding scraps little-to-no material, allowing the manufacturer to purchase significantly less materials to achieve the same volume of production.
– Reduced operational expenses
Costs are reduced by eliminating the need for the gases, filler materials, and fluxes that are required in fusion welding methods. Machining costs are also reduced by lowering tools costs and increasing productivity.
4. High Weld Integrity
Inertia friction welding is a solid-state welding process that allows no possibility for gas porosity or slag inclusions.
Friction welding creates a 100% bond of the contact area, creating joints that are equal in quality to forged bonds. The weld properties are superior to welds created with traditional fusion processes, such as MIG or TIG welding.
The process ultimately creates joint strength that is comparable or even greater to the parent materials.
5. No Quantity Limitations
Inertia friction welding is a cost-effective solution for producing prototype, small runs or large, repeated runs for ongoing projects.
6. Safety of Workers
The elimination of hazardous bright light and splattering molten material significantly decreases the risk of injuries on the floor.
How Inertia Friction Welding Is Best Used
While inertia friction welding is an extremely useful, cost-effective method of joining metals and other materials, it is not suitable for all applications and has a short set of limitations:
- Materials must be malleable at high temperatures
- Limitations arise with the presence of a brittle phase in the structure (e.g. in materials such as graphite, manganese sulfide, free lead, or tellurium)
- Cast iron is excluded from the list of weldable materials
- Bronzes and brasses are excluded from the list when they have a high lead content (> 0.3%)
- Angular orientation of welded parts is not feasible at this time
- The basic joint must be a butt weld
- In general, the joint face on at least one of the parts must be essentially round in shape
Read this guide for more information on how inertia friction welding works.
Applications That Benefit From Inertia Friction Welding
1. Roller Manufacturing
The inertia friction welding process reduces costs and cycle time for manufacturers that rely on industrial rollers.
- Nip rollers: Nip rolls are powered rolls used to press two or more sheets together, forming a laminated product. The pressure created at the nip point brings the sheets into contact, and squeezes out bubbles or blisters.
- Feed rollers: On a sheet-fed printing press, a feed roller is one of a set of rubber wheels that transports a sheet of paper from the pile table to the grippers.
- Heat transfer rollers: Heat transfer rollers provide temperature control by circulating heated or cooled fluid through coils under the outer shell of the roll. The fluid cools or heats the roll surface to the desired temperature for the application.
- Conveyor rollers
- Pressure/Fuser rollers
2. Drilling and Mining
Read a case study on using Inertia Friction Welding to create drilling rods for a company in the natural gas mining industry:
- Oil drilling
- Natural gas drilling
- Water well drilling
3. Aerospace Components that Require High-Strength Metals
4. Pneumatic Pressure Assemblies
Learn More About Inertia Friction Welding
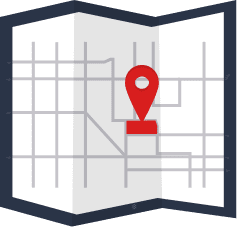
Find your local Enbi facility to enquire about our manufacturing options

Urgent technical question? Contact our experienced engineers for advice.