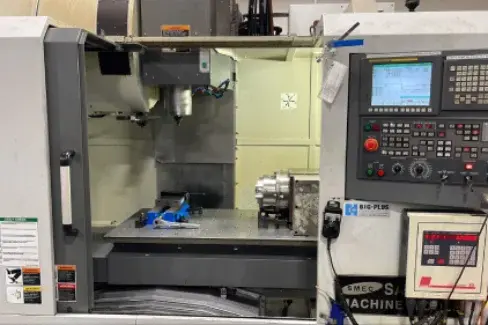
Do you feel like your time, money, and management attention are tied up worrying about quality? One way to avoid buying low quality industrial rollers for your printing and material handling machines is to address inertia friction welding quality control.
Start with Inertia Friction Welding
Today, it’s hard to compete in the printing and material handling OEM market if you aren’t building your rollers with inertia friction welding. If you’re not taking advantage of the inertia friction welding process, that’s the first place you should start.
Next Is Quality Control
If you are having your rollers built by a friction welder and still get low quality subassemblies, that’s when you should focus on quality control. Your inertia friction welding process should include these main areas of quality control: 1. Inspection, 2. Validation, 3. Data, and 4. Analytics. Monitoring these areas are vital to the performance and longevity of your product.
What Are ISO Quality Standards?
While most friction welders provide visual inspection and validation, some don’t provide data and analytics in accordance with ISO quality standards. What are ISO quality standards? Let’s take a look at an example. Enbi holds an ISO 9001:2015 certificate for maintaining a quality management system. These standards require organizations to demonstrate a quality management system that:
Consistently provides products and services that meet customer/regulatory requirements
Enhances customer satisfaction through effective application, improvement, and compliance with customer/regulatory requirements
Making sure that you partner with a roller provider that adheres to ISO quality standards is sure to increase equipment quality.